Power tools and work processes are a common source of exposure to hand arm vibration in many industries. Regular and prolonged exposure can lead to long term serious disabling health effects for exposed individuals. Conditions include hand-arm vibration syndrome (HAVS) and carpal tunnel syndrome (CTS).
The Control of Vibration at Work Regulations 2005 establish exposure limits and action levels and what should be done to manage exposure, but what do they mean in practice?
The HSE produce Inspection and Enforcement guidance for their inspectors and visiting officers which set out the framework for them to follow when assessing compliance and deciding what enforcement action to take.
In their latest guidance to inspectors for assessing how an employer is managing exposure to hand arm vibration the HSE set out a three step approach.
The first step is to make an assessment of the level of vibration exposure, this involves assessing both vibration levels and the length of time people are exposed.
The next step is then to assess the action the employer is taking to manage exposure and whether this will eliminate or reduce exposure to as low as is reasonably practicable.
The final step is to determine what, if any, enforcement action needs to be taken.
The guidance identifies several factors that and inspector should consider. Some key points are summarised below.
The first of these is whether the employer has carried out a suitable and sufficient risk assessment. A risk assessment should:
• Identify those employees who are at risk
• Make a reasonable estimate of actual exposure and compare this with the action and limit values set out in the legislation
• Consider health surveillance
• Identify action to be taken to control risk
• Be regularly reviewed
Where exposure is likely to exceed the action value set out in the legislation, the employer should, where reasonably practicable, identify and adopt industry best practice for eliminating or reducing exposure. Note: daily exposure to vibration should not exceed the limit value set out in the legislation, and action will need to be taken where this is likely.
Where exposure can’t be eliminated then action should be taken to or reduce exposure to as low as is reasonably practicable, examples include:
• Selecting suitable equipment for the job
• Designing the work to reduce grip and push forces
• Maintaining tools and equipment
• Limiting daily exposure e.g. by limiting time spent on particular jobs
• Providing gloves and clothing to keep workers warm and dry
Where required suitable occupational health surveillance should be provided, including initial screening for people who are new to the work. Responses that indicate symptoms should be referred to an occupational health specialist and further escalated as appropriate.
Advice from the occupational health specialist should be followed, removing employees from work that exposes them to vibration if they are identified as not fit to work.
Employees should also be provided with suitable information, instruction and training which should cover vibration risks and how to reduce them, the importance of maintenance and correct operation of tools, signs and symptoms of HAVs and how to report them and arrangements for health surveillance.
Guidance for inspectors on a wide range of topics can be found on the HSE’s website at: https://www.hse.gov.uk/foi/internalops/og/index.htm
Our specialists can help you to carry out hand-arm vibration risk assessments and manage exposure at your workplace. Please speak to your normal PIB Risk management contact or get in touch using [email protected] if you have any questions or would like to arrange an assessment for your workplace.
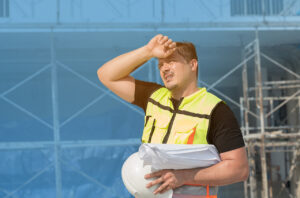
The Sun’s Out – Time To Get The Shorts Out?
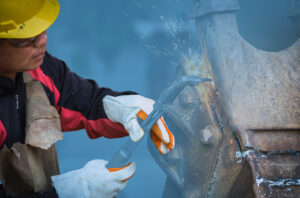
Updated Gas Safety Guidance
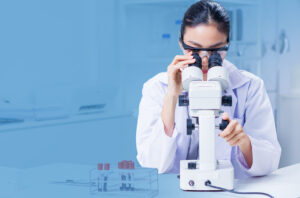
Revised Bloodborne Viruses Guidance
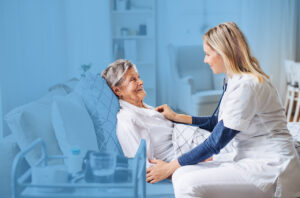
New High Consequence Infectious Disease Guidance for Care Providers
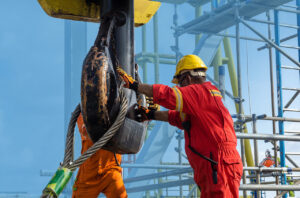
New Guidance On The Safe Rigging Of Cranes
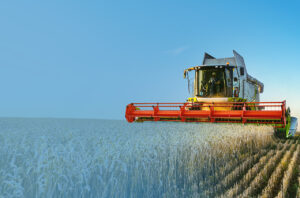